HS4000 II | HS5000 II
The HS4000/5000II CNC Horizontal Center is designed on a high-precision structure, high-speed integrated shaft and rigid guide system, raising accuracy and reducing thermal deformation when machining parts.
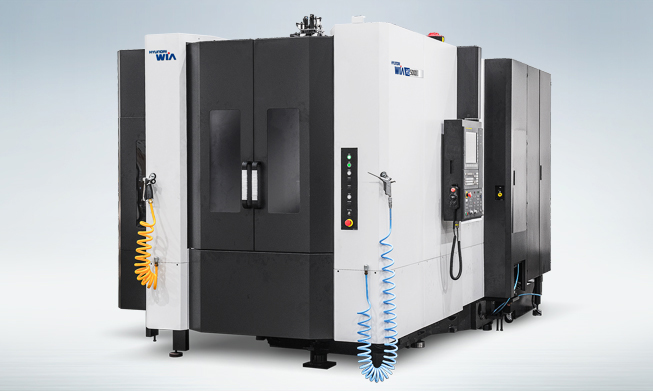
- HS4000/5000II Horizontal Machining Center have 15,000 rpm high-performance built-in spindle
- X/Y/Z axis rapid traverse rate : 60m/min
- Ball screw shaft cooling system applied
- High rigidity 3-point support bed structure
- Large dia. Ø50 mm (2″) ball screw applied
- Ring type magazine standard application
- 60T magazine Max call time : 2.9 sec
- Best-in-class tool change time (c-c) : 2.6 sec
Structure
3-point Support Bed Structure
The HS4000/5000II Horizontal Machining Center Series is the first series of the company to apply the three-point support bed which is a criteria for high-rigidity structure.
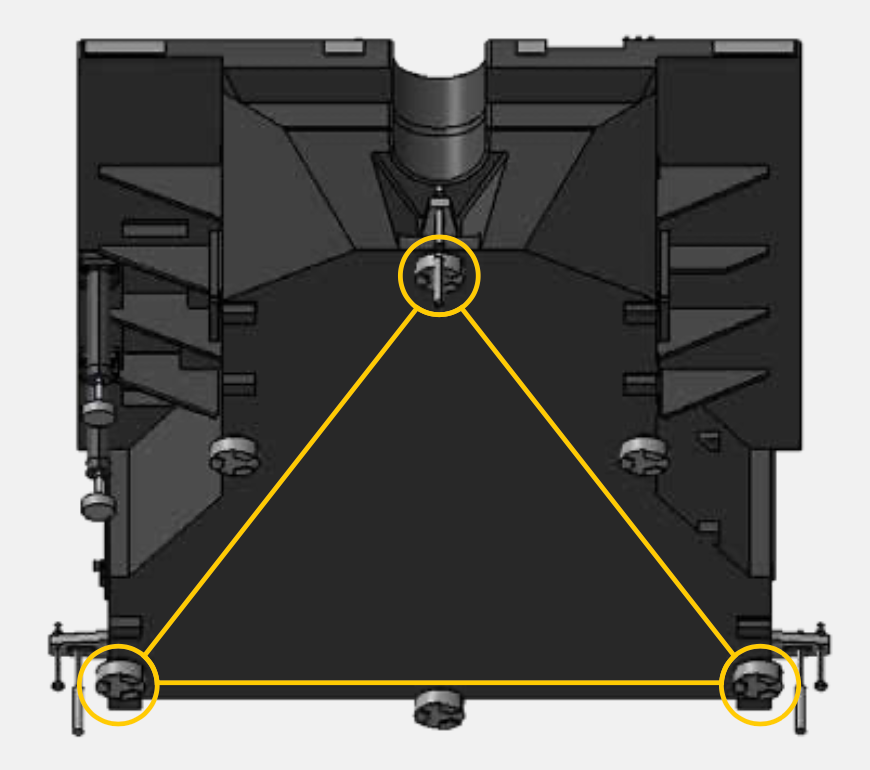
The three-point support bed is a structure that allows easy machiningas long as the three levels at the bottom of the bed are stabilized during initial setup, and such machining is only available with support from structural rigidity of the machine. Initial construction is especially not necessary during initial setup and this can minimize the equipment setup time which makes it every efficient for use of equipment.
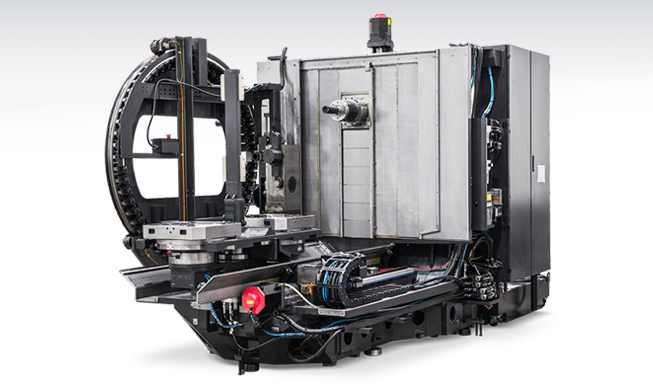
Step Type Bed Structure
Step-type bed was applied to sufficiently withstand the thrust generated from Z-axis machining. Furthermore, stability was improved even more with the low center of gravity design of the feeding related unit.
Optimal structural analysis
optimal structure through the unique structural analysis of Hyundai-WIA. Also, the column has become stiffer, even if it is lighter in weight compared to the previous model.
Guideway
Linear guide with high speed rollers
Linear roller guides are applied to reduce cutting time and increase rigidity. Each shaft is directly connected to an extremely reliable digital servomotor to provide high rigidity and minimal thermal deformation.
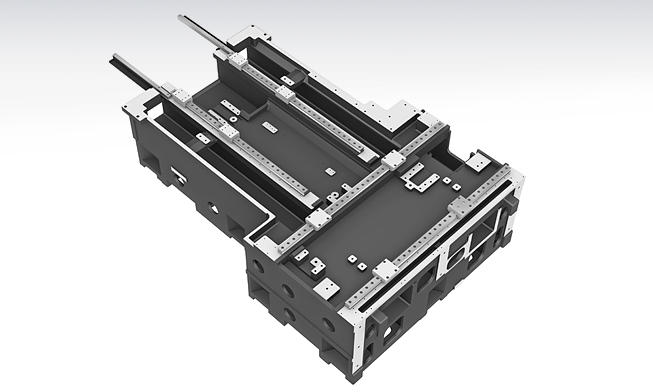
Double anchored ball screw
The strokes are stabilized by fixing both ends of the ball screw using the double-anchored method. Large ball screw (type “M”) The large diameters of all ball screws allow high accuracy even during heavy cutting.
The prestressed ball screw reduce heat expansion and contraction and further strengthens the rigidity by the double anchor support method. In addition, the coupling of ball screws and highly reliable digital actuators are connected by couplings with metal plates, to reduce coupling breakage and play
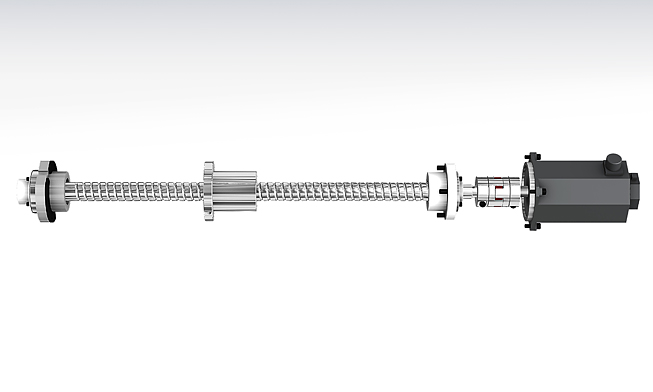
Ball screw with cooling nuts
Balls screw with cooling nuts on all axes reduce thermal deformation, which increases machining accuracy.
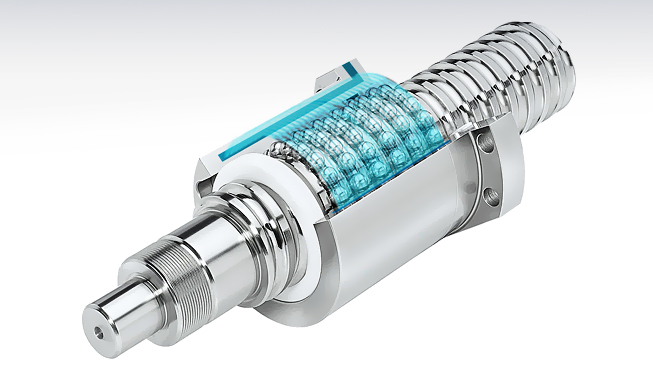
Spindle
High-performance Built-in Spindle
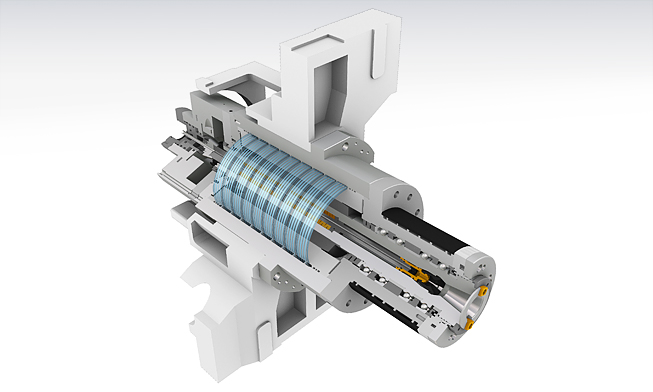
The HS-II Series has applied a standard built-in spindle of 15,000 rpm to respond to high-speed machining. The built-in spindle capable of 15,000 rpm consists of standard specifications of 30kW (40HP)/230N.m (169.6 lbf.m) and 37kW (50HP)/303N.m (223.5 lbf.m) for customers to be able to select the spindle based on their machining conditions.
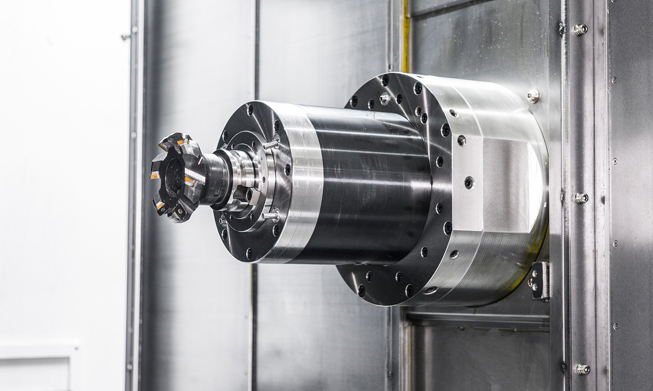
Chip Stack Prevention Coolant on the Upper Part of the Spindle
Chip stack prevention coolant is applied as a standard on the upper part of the spindle to create a pleasant working environment.
Oil cooling system
Shaft temperature is controlled by using an oil cooler. This ensures a constant temperature of the shaft, which reduces thermal deformation.
Through Spindle Coolant
Through Spindle Coolant is exceedingly useful when drilling deep holes. It helps increase the lifetime of the tool, while decreasing cycle time.
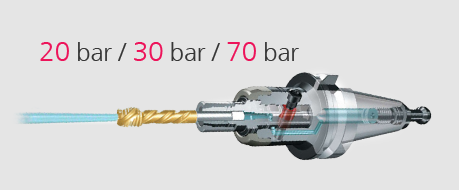
Double tool holder contact
shaft and face of the tool holder flange. Increasing the standard diameter improves the rigidity and repeatability of the ATC, and the displacement of the Z axis is prevented, which prolongs the tool life.
HSK tool holder
The HSK tool holder is dimensioned for precise positioning with a lower clearance in the taper of the shaft during high speed rotation. This ensures an excellent level of precision for high precision machining.
Tool Magazine
Ring Type Magazine
The HS-II series has a ring type magazine as standard. The ring type magazine makes less noise than the existing chain type and has faster rotation of the magazine, which contributes to reduced tool exchange time and improved productivity.
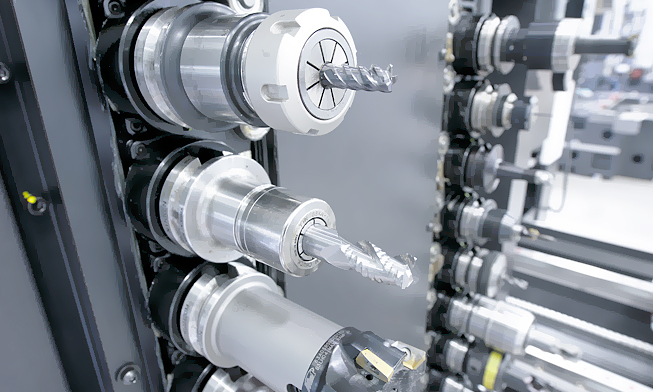
Front Placement of the Magazine for Worker Convenience Magazine installed at the side was installed at a location which is closest possible to the front door to improve material and tool exchange convenience.
Ring Type | Chain Type | Matrix Type |
40, [60] | [90, 120] | [240] |
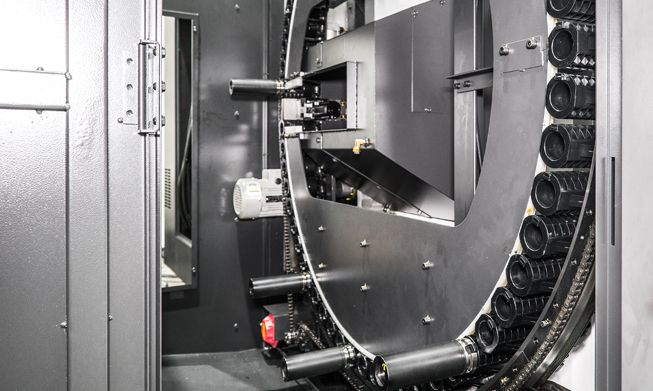
High-performance APC
High Speed & Rigidity APC
The HS-II Series contributes to improvement in productivity by reducing the APC exchange time and increasing rigidity compared to the previous model.
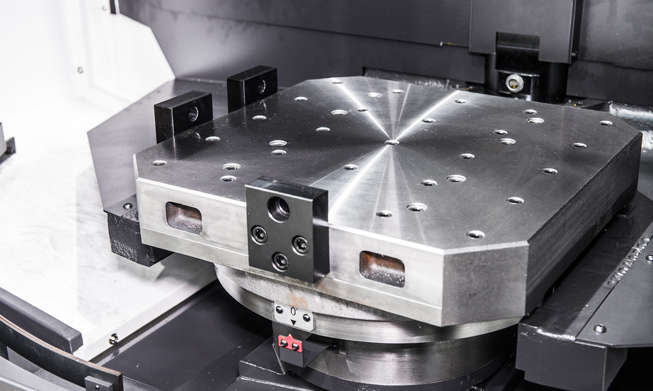
Roller Gear Cam Type 0.001˚ Pallet
The pallet rotation for the previous model of the company and other equipment from different manufacturers operated by the worm gear method but the 0.001˚ pallet which comes as an option for HS4000 II operates by the roller gear cam method. The roller gear cam method features less power loss from smooth movement along the cam curve, and it is more advantageous for high-speed rotation due to generating less friction from rotation of the roller rather than the gear.
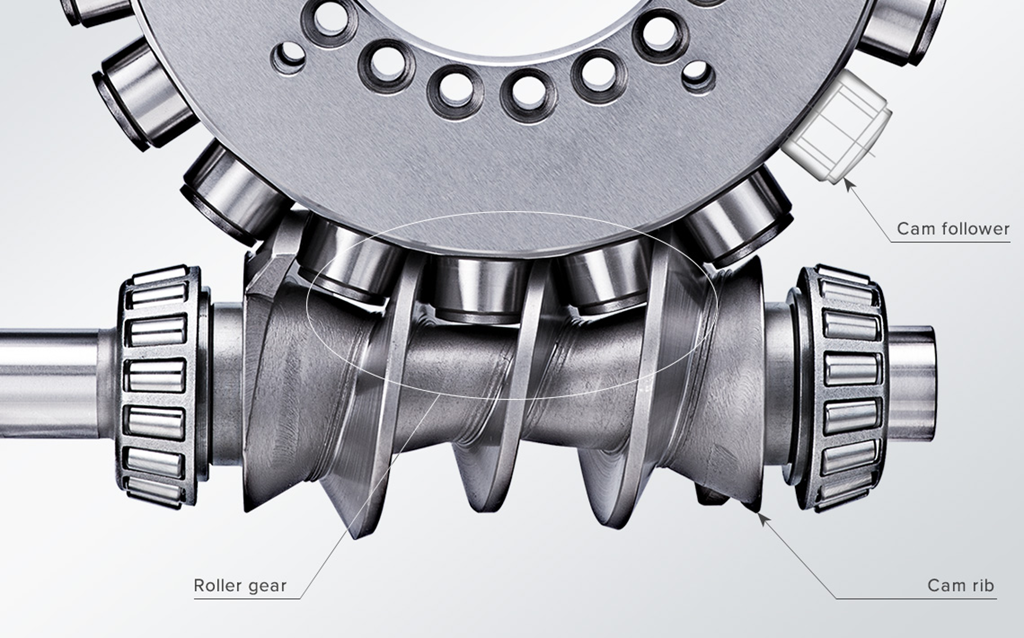
Chip Disposal
Direct Chip Discharge Structure
The structure was designed for the chip to fall directly to the center of the bed to improve chip discharge capability, and the lack of necessity for a separate internal screw conveyor fundamentally eliminated the chip trouble from the internal screw conveyor.
Video HS6300 & L400C
Technical Specifications HS4000 II
Table Size [mm] | 2 – 400×400 |
Max. Load Capacity [kg] | 2 – 400 |
Spindle Driving Method | Built in |
Spindle Taper | BBT40 |
Spindle RPM [r/min] | 15,000 |
Spindle Power [kW] | 30/18.5 |
Spindle Torque [Nm] | 230/119 |
Travel(X/Y/Z) mm | 730/730/880 |
Rapid Feed Rate(X/Y/Z) [m/min] | 60/60/60 |
Slide Type | LM |
No. of Tools | 40 |
No. of Pallets | 2 |
Technical Specifications HS5000 II
Table Size [mm] | 2 – 500×500 |
Max. Load Capacity [kg] | 2 – 500 |
Spindle Driving Method | Built in |
Spindle Taper | BBT40 |
Spindle RPM [r/min] | 15,000 |
Spindle Power [kW] | 30/18.5 |
Spindle Torque [Nm] | 230/119 |
Travel(X/Y/Z) mm | 730/730/880 |
Rapid Feed Rate(X/Y/Z) [m/min] | 60/60/60 |
Slide Type | LM |
No. of Tools | 40 |
No. of Pallets | 2 |