HS6300 | HS8000
The HS6300/8000 CNC horizontal center is designed on a high-precision structure, high-speed integrated shaft and rigid guide system, raising accuracy and reducing thermal deformation when machining parts.
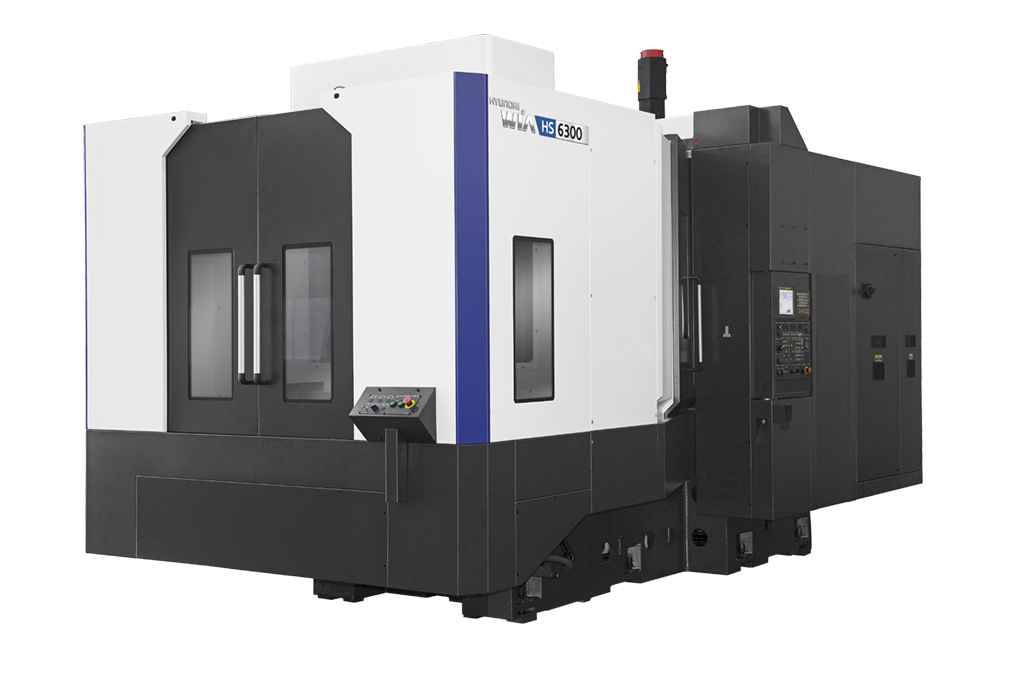
- HS6300/8000 Horizontal Machining Center have High-speed, High-rigidity Roller Guides on all axes
- 2 Step Gear spindle for heavy duty cutting
- High-speed, Built-in Main Spindle (12,000rpm, optional)
- Big Plus Spindle is standard
- Minimized footprint for Optimal Layout
Structure
Reverse “T” Type Bed
The ‘T’ structure of the bed is designed with ample bed height and casting thickness to ensure the optimal level of rigidity.
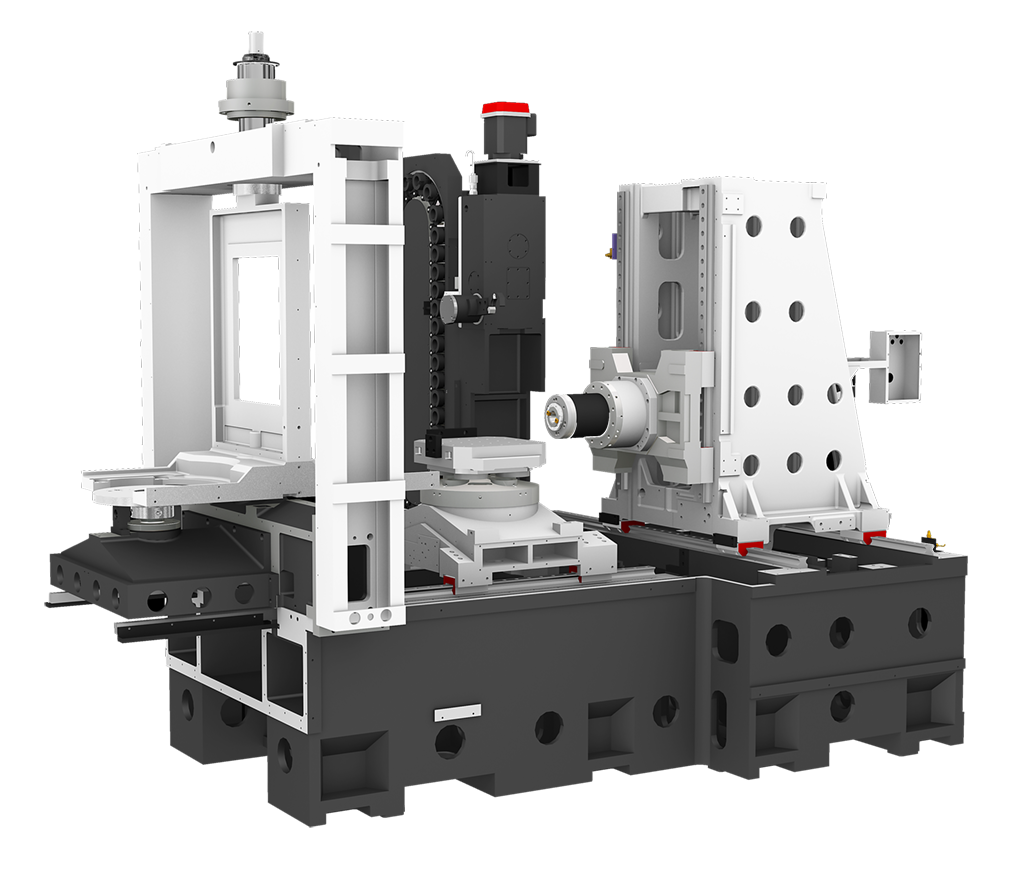
Step Type Bed Structure
Step-type bed was applied to sufficiently withstand the thrust generated from Z-axis machining. Furthermore, stability was improved even more with the low center of gravitydesign of the feeding related unit.
Optimal structural analysis
optimal structure through the unique structural analysis of Hyundai-WIA. Also, the column has become stiffer, even if it is lighter in weight compared to the previous model.
Guideway
Linear guide with high speed rollers
Linear roller guides are applied to reduce cutting time and increase rigidity. Each shaft is directly connected to an extremely reliable digital servomotor to provide high rigidity and minimal thermal deformation.
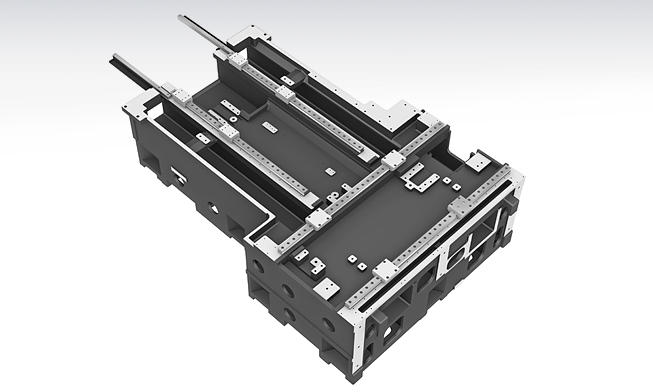
Double anchored ball screw
The strokes are stabilized by fixing both ends of the ball screw using the double-anchored method. Large ball screw (type “M”) The large diameters of all ball screws allow high accuracy even during heavy cutting.
The prestressed ball screw minimizes heat expansion and contraction and further strengthens the rigidity by the double anchor support method. In addition, the coupling of ball screws and highly reliable digital actuators are connected by couplings with metal plates, to reduce coupling breakage and play
Ball screw with cooling nuts
Balls screw with cooling nuts on all axes reduce thermal deformation, which increases machining accuracy.
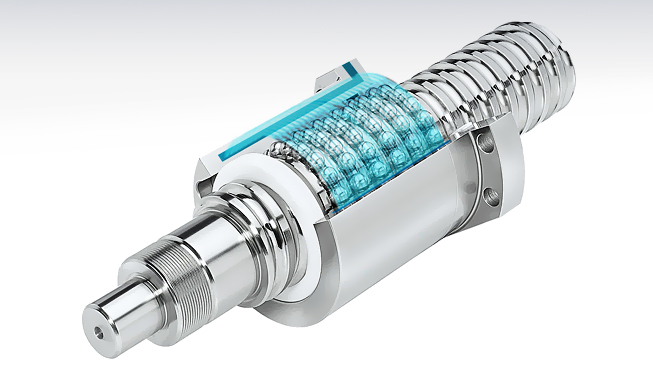
Spindle
Gear Type Spindle
the gear type spindle provides powerful torque at low speeds
and stable rotation at high speeds and this enables wide range
of machining. The spindle uses angular ball bearings and is designed to maximize rigidity. Also, powerful tool clamping force improves cutting ability. The AC spindle motor with max. power of 22kW(29.5HP) and max. speed of 8,000rpm is suitable for heavy duty cutting and high speed machining. The spindle’s oil cooling system is designed to minimize thermal displacement.
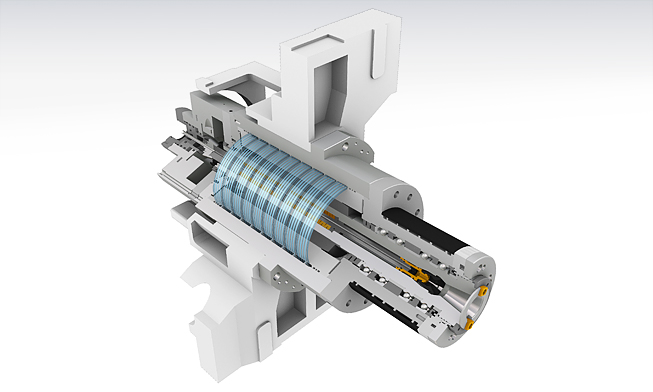
Built-in Spindle
By using ultra precision class angular ball bearings, fast acc/
deceleration of the main spindle is achieved. The spindle head is
designed to minimize heat displacement therefore reducing heat generation and making it possible to maintain high accuracy. Spindle temperature is controlled by the using spindle oil chiller
Through Spindle Coolant
Through Spindle Coolant is exceedingly useful when drilling deep holes. It helps increase the lifetime of the tool, while decreasing cycle time.
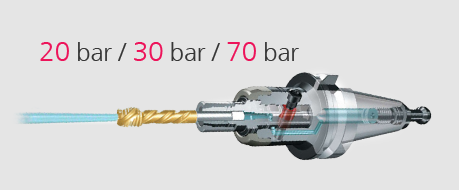
Dual Contact Spindle
The Big Plus spindle system (BBT#50) provides dual contact between the spindle face and the flange face of the tool holder.
ATC & Magazine
The tool magazine holds 40 tools as standard and up to 120 tools as an option depending on the model. Servo control, fixed address tool selection method and a separate magazine control panel enhance user convenience. The twin arm ATC provides fast and reliable tool change to reduce noncutting time.
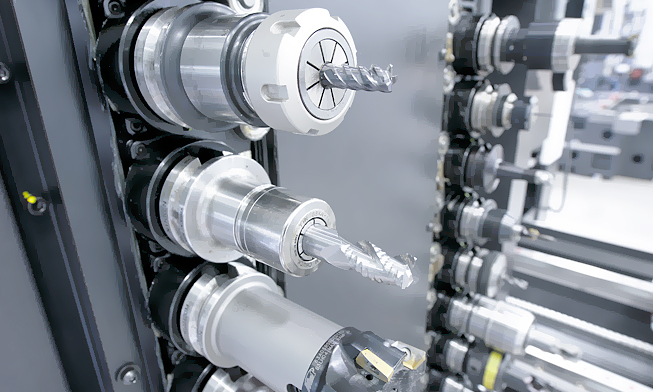
APC & Pallet
HS6300/8000 provides a rotary shuttle APC (automatic pallet changer) as standard. The loading station pallet can be rotated and locked in 90° increments for convenient loading/unoading of workpieces.
Locating cones at the positioning base are used for pallet clamping. Inside the cones, there are clamping devices for powerful clamping of pallets which is suitable for heavy duty cutting. 1° index table is applied with high precision curvic coupling for accurate indexing.
Air Clearing System
During the pallet change cycle, strong air blasts from the taper cones on the machine table help remove chips and provide a clean surface for locating the pallet. This ensures high accuracy of pallet positioning and guarantees optimum rigidity.
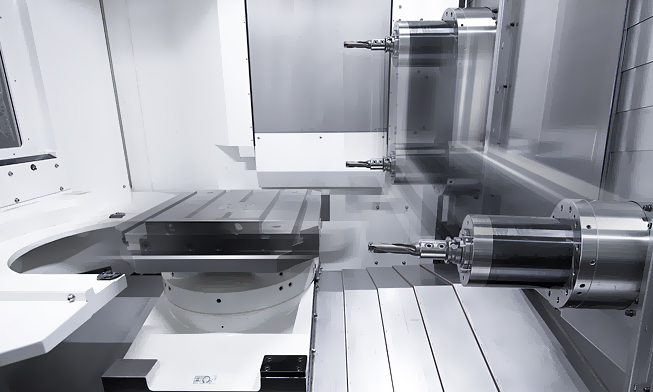
Technical Specifications HS6300
Table Size [mm] | 630×630 |
Max. Load Capacity [kg] | 2 – 1,200 |
Spindle Driving Method | GEAR |
Spindle Taper | BBT50 |
Spindle RPM [r/min] | 8,000 |
Spindle Power [kW] | 22/18.5 |
Spindle Torque [Nm] | 781/657 |
Travel(X/Y/Z) mm | 1,050/875/875 |
Rapid Feed Rate(X/Y/Z) [m/min] | 50/50/50 |
Slide Type | LM |
No. of Tools | 40 |
No. of Pallets | 2 |
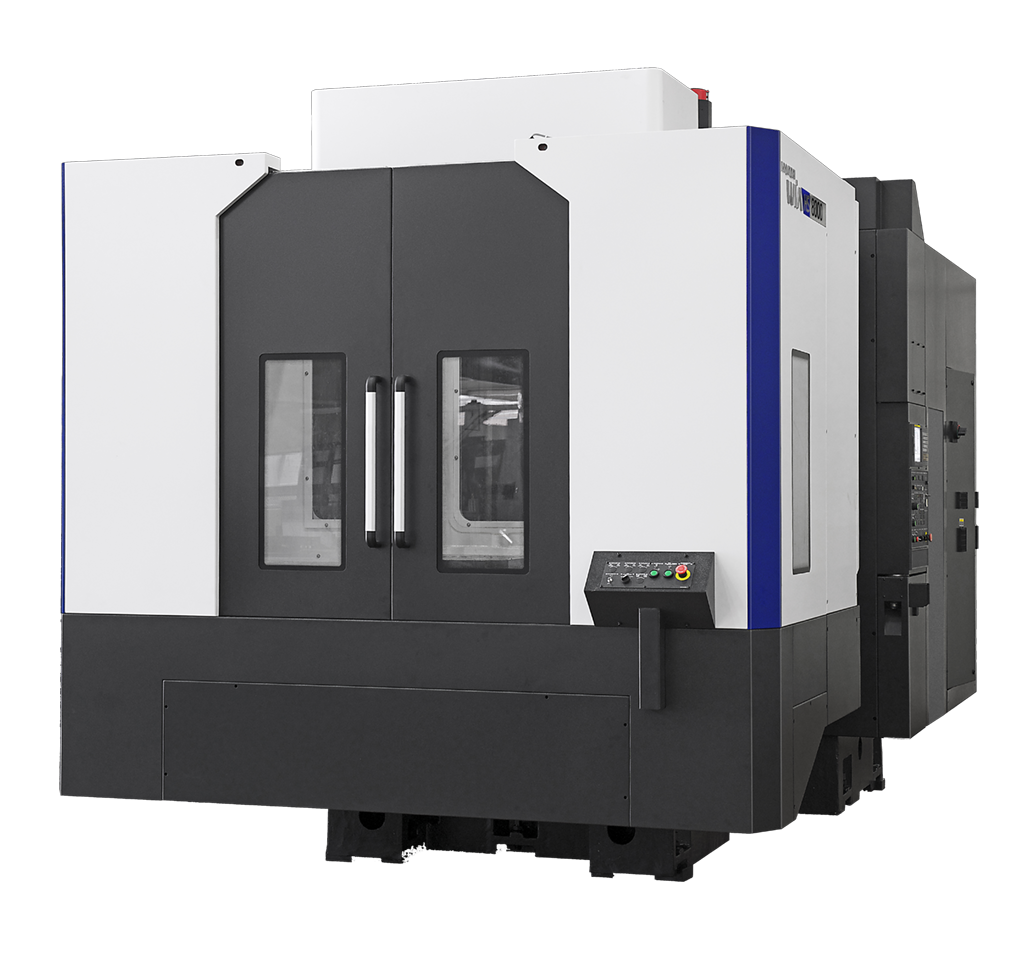
Technical Specifications HS8000
Table Size [mm] | 800×800 |
Max. Load Capacity [kg] | 2 – 1,600 |
Spindle Driving Method | GEAR |
Spindle Taper | BBT50 |
Spindle RPM [r/min] | 8,000 |
Spindle Power [kW] | 22/18.5 |
Spindle Torque [Nm] | 781/657 |
Travel(X/Y/Z) mm | 1,050/875/875 |
Rapid Feed Rate(X/Y/Z) [m/min] | 50/50/50 |
Slide Type | LM |
No. of Tools | 40 |
No. of Pallets | 2 |